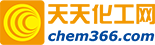
在全球碳中和目标加速推进的背景下,聚氨酯(PU)行业正迎来一场深刻的绿色革命。作为建筑、汽车、电子、纺织等领域不可或缺的高分子材料,聚氨酯的传统生产模式正面临环保政策收紧与市场需求转型的双重挑战。行业数据显示,2023年全球聚氨酯市场规模已突破800亿美元,但与此同时,石油基原料依赖度高、碳排放强度大、废弃物回收难等问题日益凸显。在此背景下,生物基原料研发、化学回收技术突破以及低碳工艺创新成为行业突围的关键路径,一场以可持续发展为核心的产业变革正在展开。
一、政策倒逼转型:全球监管趋严加速技术迭代
近年来,全球范围内针对化工行业的环保政策密集出台,聚氨酯产业链首当其冲。欧盟《可持续化学品战略》明确要求,到2030年,聚氨酯生产过程中的化石原料使用量需减少30%,并将生物基材料替代率纳入企业ESG评级体系。中国《“十四五”塑料污染治理行动方案》则提出,推动聚氨酯等重点领域开展全生命周期碳足迹管理,对挥发性有机物(VOCs)排放和废弃物资源化率提出更高要求。
政策压力下,行业技术路线加速重构。多家头部企业已宣布将生物基聚醚多元醇产能提升至总产量的20%以上,部分领先厂商甚至通过碳捕获技术,将工业尾气转化为聚氨酯原料,大幅降低对石油资源的依赖。与此同时,国内新建聚氨酯项目普遍引入智能化控制系统,通过工艺优化使单位能耗下降15%-20%,VOCs排放量减少超30%。
二、生物基材料崛起:从实验室走向规模化生产
生物基聚氨酯的商业化进程正在打破行业固有格局。据最新市场报告,2023年全球生物基聚氨酯市场规模同比增长18%,其中亚洲地区增速领跑全球,主要得益于农业废弃物资源化利用技术的突破。目前,以蓖麻油、玉米秸秆、微藻油脂等为原料的生物基多元醇已实现规模化生产,部分产品性能甚至超越传统石油基材料。
技术层面,合成生物学为行业注入新动能。通过基因编辑技术定制的高效菌株,可将葡萄糖、木质纤维素等生物质高效转化为聚氨酯关键单体,生产成本较传统化学法降低近40%。例如,某国内研究团队开发的蓖麻油基弹性体材料,其耐老化性能提升20%,已成功应用于新能源汽车零部件制造;另一项稻壳提取木质素合成硬质泡沫的技术,则使保温材料的导热系数突破0.019W/(m·K),刷新行业纪录。
值得注意的是,生物基聚氨酯的应用场景正从传统领域向高端市场延伸。具备天然抗菌性的腰果壳油基涂料、可降解的食品包装薄膜等创新产品,已进入医疗、消费电子等高附加值领域,推动行业利润率提升5-8个百分点。
三、循环经济破局:化学回收技术打通“最后一公里”
聚氨酯废弃物处理曾是行业痼疾。由于材料交联结构复杂,传统物理回收法仅能处理10%-15%的废料,且产物性能大幅衰减。近年来,化学回收技术的突破彻底改变了这一局面。糖酵解、超临界醇解等工艺可将废旧泡沫、弹性体等材料高效解聚,再生多元醇纯度可达99%以上,完全满足高端产品生产需求。
行业数据显示,2023年全球聚氨酯化学回收产能同比增长45%,欧洲某领先企业建设的万吨级回收工厂,每年可处理20万张废旧床垫,减少碳排放约5万吨。国内科研机构研发的“解聚-重聚”一体化技术,更是将软质泡沫回收率提升至90%以上,相关生产线已在长三角地区落地。更具前瞻性的是,可逆交联型聚氨酯材料的问世,使得产品在寿命结束后可通过简单催化实现“一键还原”,真正实现闭环循环。
四、新兴需求爆发:千亿级市场蓝海显现
在技术创新与政策红利的双重驱动下,聚氨酯的应用边界持续拓展:
新能源领域:轻量化趋势推动聚氨酯结构胶需求激增,动力电池包用微孔发泡材料市场规模年增长率超25%,兼具阻燃与减震性能的新品成为竞争焦点;
智能穿戴设备:热塑性聚氨酯(TPU)凭借高弹性与生物相容性,成为柔性传感器、电子皮肤的核心材料,预计2025年相关应用市场规模将突破60亿美元;
绿色建筑:零臭氧消耗潜能(ODP)、低全球变暖潜能(GWP)的聚氨酯保温系统市占率快速提升,光伏一体化墙体解决方案节能效率较传统材料提高40%以上。
五、挑战与未来:成本、标准与协同创新待突破
尽管前景广阔,行业仍面临现实瓶颈。生物基聚氨酯原料成本较石油基产品高出20%-50%,且受农作物产量波动影响明显;化学回收工厂建设成本高昂,中小企业普遍面临资金与技术双重壁垒。此外,各国生物基含量认证标准不一,导致国际贸易摩擦风险上升。
对此,行业专家建议构建“政产学研用”协同创新体系:通过碳税杠杆缩小成本差距,建立覆盖原料种植、生产制造到回收再生的全生命周期标准;同时加快关键催化剂、高效分离膜等核心技术攻关,推动产业链上下游协同降碳。
可以预见,随着全球ESG投资标准趋严与低碳技术迭代加速,聚氨酯行业的绿色转型已不可逆转。那些在生物基材料、循环技术、低碳工艺等领域提前布局的企业,将在这场价值重塑中占据先机,而这场变革或将重新定义高分子材料产业的未来图景。